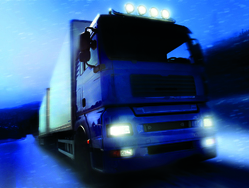
A partire da quelle più semplici per finire a quelle dedicate ai veicoli elettrici, le batterie per veicoli industriali sono componenti fondamentali per garantire l’efficienza di un veicolo e, più in generale, di una flotta. Cosa vale la pena sapere? Ve lo raccontiamo qui di seguito.
In queste pagine, ci concentreremo su tutte quelle situazioni critiche che coinvolgono gli accumulatori impiegati nel settore dei trasporti, tralasciando l’argomento, ancora più complesso, delle batterie dedicate ai veicoli elettrici. Nel seguito, daremo per scontato il principio di funzionamento di una batteria.
Batterie con tecnologia EFB e con tecnologia AGM
Prima di procedere ad approfondire le tematiche strettamente legate al mondo delle batterie, e a quello delle relative applicazioni, vale la pena parlare di due tecnologie oggi molto diffuse nel campo degli accumulatori utilizzati nel mondo dei trasporti.Le batterie con tecnologia EFB (Enhanced Flooded Battery) sono componenti introdotti in tempi relativamente recenti per consentire ai costruttori di ottemperare alle stringenti normative in termini di emissioni. Sono batterie che devono garantire un ciclo di vita elevato. I costruttori generalmente richiedono per questo tipo di batterie una durata di 200 cicli con batteria al 50% della propria capacità. Solitamente, questo dato di targa viene indicato con una dizione del tipo: 200 cicli con 50% DOD (Depth of Discharge). Ne parleremo ulteriormente più avanti in questo stesso articolo.
Le batterie con tecnologia AGM (Absorbed Glass Mat), invece, sono componenti con separatori realizzati in fibra di vetro puro (il glass mat) compresso in luogo dei più tradizionali in polietilene. Sono batterie pensate per veicoli industriali e commerciali con un fabbisogno energetico elevato. Senza entrare eccessivamente nei dettagli costruttivi, si tratta di un sistema costruttivo che permette di ottenere una compressione maggiore dei pacchetti di celle, aspetto che, oltre a migliorare la durata, consente di elevare l’efficienza del processo di ricombinazione dei gas. Non richiedono quindi manutenzione.
Le batterie AGM hanno permesso ai costruttori di rivedere completamente la strategia di funzionamento dell’alternatore, mantenendolo spento per più tempo, anche a costo del raggiungimento di una scarica superiore della batteria stessa.
La batteria giusta per ogni applicazione
Le batterie non sono tutte uguali, ovviamente, ma anche quelle che possono sembrare simili in realtà non lo sono, perché la tecnologia delle batterie è un argomento complesso e tutt’ora oggetto di studio.Oggi, i produttori progettano le proprie batterie per tener conto dei costi totali di gestione, il famoso indice TCO (Total Cost of Ownership). E per farlo vengono utilizzati dei modelli che sono in grado di tener conto di una molteplicità di parametri, come i costi iniziali, i costi di manutenzione, la durata stessa della batteria e la probabilità che si verifichi un’avaria. Ed è proprio in questa direzione che viene orientata tutta la tecnologia delle batterie più tradizionali (qui definite in questo modo per distinguerle da quelle dei veicoli elettrici).
A seconda dell’impiego, le batterie offriranno caratteristiche diverse. È evidente come possa essere completamente differente la missione delle batterie montate su mezzi dedicati alle lunghe percorrenze, dove gli accessori di bordo, che assorbono energia, sono numerosi e sempre più complessi, rispetto a quelle invece installate su mezzi impiegati in condizioni più estreme e su percorsi accidentati, ma con una missione molto più circostanziata. Per non parlare delle condizioni ambientali in cui il mezzo si trova ad operare.
Una batteria di ultima generazione deve quindi essere in grado di soddisfare molte altre caratteristiche tecniche: deve potersi caricare velocemente, ma allo stesso tempo deve mantenere inalterata la sua funzionalità, anche dopo una lunga serie di cicli di lavoro (carica e scarica). In altre parole, deve sempre mantenersi su livelli accettabili la stratificazione dell’acido che a lungo andare provoca una perdita di capacità della batteria stessa.
È quindi interesse sia dei costruttori sia dei produttori di batterie riuscire a realizzare accumulatori con capacità di ciclaggio sempre maggiori. Per ottenere questo risultato ogni produttore ha cercato una suo strada, proponendo soluzioni sempre più interessanti che in prima battuta riguardano il primo impianto, ma che hanno ricadute dirette anche sui prodotti aftermarket.
Una delle soluzioni, per quanto riguarda le batterie EFB, ad esempio, è quella di ricorrere a strati di lana di vetro sulla materia attiva (la fibra di vetro di cui abbiamo già detto). In questo modo le performance di ciclaggio aumentano notevolmente, arrivando anche a 200 cicli al 50% della Depth of Discharge, dove, ricordiamolo, 200 è il numero dei cicli che la batteria può sopportare con stato di carica al 50%. Risultati importanti che sono ottenuti anche grazie a soluzioni sulle griglie,che possono essere inserite in dei box rinforzati e con separatori specifici ad alta densità così da mantenere la lana di vetro sulla materia attiva.
Un’altra via operata nella produzione di primo impanto e disponibile anche in aftermarket è quello di inserire negli accumulatori dei sistemi definiti circolatori dell’acido. In questo modo si rallenta il processo di stratificazione dell’acido tipico delle scariche profonde. Si tratta di un elementi strutturali che sfruttano il movimento naturale del veicolo per assicurare la circolazione continua dell'acido all’interno della batteria. La densità dell'acido rimane così omogenea.
Il trend d’altronde è chiaro: i camion moderni stanno diventando sempre più sofisticati, ponendo nuove sfide alla batteria. Allo stesso tempo, le aziende vogliono ridurre i costi, aumentare l’affidabilità e la disponibilità. La scelta della giusta batteria, quindi, può fare una grande differenza per qualsiasi azienda, soprattutto nell’attuale mercato.
Anche la posizione conta
Le stringenti normative sulle emissioni stanno cambiando un po’ tutto il panorama progettuale dei veicoli pesanti. Per passare agli standard Euro V e Euro VI, alcuni costruttori hanno introdotto il sistema della Riduzione Catalitica Selettiva (SCR), soluzione che ha portato a una rivisitazione del layout per la disposizione dei componenti.A rimetterci, in un certo senso, sono state proprio le batterie, che ora si trovano spesso riposizionate in zone del telaio soggette a vibrazioni molto più elevate, aspetto di cui ogni produttore di batterie di oggi deve assolutamente tener presente. Sempre più spesso, le troviamo installate in prossimità dell’asse posteriore, cosa che le rende particolarmente soggette a vibrazioni. Per questo motivo devono presentare elevata robustezza e resistenza alle vibrazioni. D’altronde è la stessa Comunità Europea che con l’introduzione della norma EN 50342-1:2015 ha fissato numerosi standard per il mondo degli accumulatori, sia per il trasporto persone sia per i veicoli commerciali e industriali. Tra i vari standard definiti, non a caso, è stato introdotto anche un parametro per la resistenza alle vibrazioni, che è codificato con sigle che vanno V1 (il minimo) a V4, la massima resistenza.
Anche in questo caso raggiungimento classificazione V4 fa parte della strategia e della modalià produttiva di ogni azienda. Una delle soluzioni, ad esempio, consiste nell’aggiungere tra la piastra e il separatore uno strato aggiuntivo. Così facendo viene realizzata una maggiore resistenza alle scariche profonde. Il materiale incollato, inoltre, blocca le piastre in posizione in qualsiasi condizione di impiego. In altri casi viene aggiunto del materiale plastico nella parte inferiore della batteria (al fine di previene la rottura della striscia conduttrice), mentre in altri casi si è deciso di intervenire sul coperchio della batteria, dove le sollecitazioni possono portare a perdite. Noto il caso di un produttore tedesco che ha adottato una soluzione a labirinto per evitare la perdita di gas ed evitare pericolosi ritorni di fiamma.
Tutte soluzioni che possono essere presenti anche contemporaneamente su un accumulatore. Per semplicità, ovviamente, il suggerimento è comunque verificare la sigla che certifica la resistenza alle vibrazioni.
Come gestire una batteria
Una batteria che si scarica quasi completamente e poi viene ricaricata con metodi errati è una delle principali cause di avaria. Anche su questo fronte, le soluzioni per gestire il problema sono da ricercarsi nel metodo e anche nella tecnologia.Anche in termini di tecnologia le soluzioni sono molte e differenti, tra le più innovative, per contrastare il rischio di scariche profonde, assicurando, parallelamente, altri benefici che ottimizzano le prestazione c’è l’utilizzo di additivi al carbonio. In questo caso è un’azienda Italiana ad aver introdotto questa tecnologia e il funzionamento sfrutta la solfatazione, e quindi la conseguente stratificazione dell’acido. In questo modo le batterie possono offrire un’accettazione di carica superiore e si ricaricano più velocemente migliorando la resistenza al ciclaggio.
Il danno più ricorrente
Un numero elevatissimo di batterie soggette a sostituzione arrivano danneggiate per una carenza di carica. La gestione errata della batteria è un male diffuso e la scarica completa (tutta la capacità della batteria viene esaurita), con un lungo periodo di fermo, porta quasi sempre a danni permanenti e perdita di ricaricabilità. Questa è una condizioni da non raggiungere mai, ma purtroppo, nell’uso comune accade spesso.Come prendersi cura della batteria
I costruttori di truck forniscono chiare indicazioni agli utenti. Per la conservazione ottimale della batteria, tra i consigli più gettonati, e non a torto, possiamo ricordare i seguenti: proteggerle dalle temperature più basse, controllare i collegamenti tra cavi e poli, che devono sempre essere in ottime condizioni, assicurarsi che non vi sia la minima dispersione (ci sono dispositivi che potrebbero sottrarre energia alla batterie anche quando sono in condizioni di riposo), mantenere le batterie completamente cariche ed evitare, se possibile, un numero troppo elevato di arresti e successive ripartenze.Tags: batteria truck